Welding is a really useful skill to learn. While some welding methods don’t require a shielding gas, they are also not as effective for every project. As you gain experience, you’re ready to learn more advanced welding methods, which will require welding gas.
Table of Contents
Key Takeaways
- In MIG (metal inert gas ) and TIG welding, shielding gases are necessary to protect your weld area from oxygen, nitrogen and water vapors
- Welding gases will also stabilize your arc and make sure your metal transfer is enhanced
- Most common shielding gases used in welding are Argon, Helium, Carbon Dioxide and Oxygen
- Depending on what you are welding, you will sometimes use a mixture of gases
- These blends are tailored to specific base and filler metals for maximum impact and weld quality overall
Not every method uses the same type of gas, though. You will need special gas for MIG welding. There are several different gases for TIG welding because TIG shielding gas can be diluted. MIG gas is simpler than TIG gas, but you still want to make sure you pick up the right MIG shielding gas.
So, what gas is used for TIG welding and how much gas is needed? Our guide will tell you all about the gas for TIG welding, as well as the different MIG welder gas options. If you’re ready to start your next weld process, but you aren’t sure what shielding gas for MIG welders, our guide can help you find that answer.
Welding Gas Types: MIG Welding Gas Versus TIG Welding Gas
When it comes to welding, no single welding process is standard across all areas of the industry.
A lot of welders have their own preferred method for handling different applications, and a wide variety of methods can all produce sound, aesthetically pleasing welds.
The process also varies based on the type of material being used, the location and available space, and the position of the joint in need of a weld. Even things like ferrous versus non-ferrous, magnetic or non-magnetic, and the final application of the metal all have to do with the type of welding procdure used. These also influence the type of gas being used.
What welding processes use gas?
There are 2 extremely common welding methods that use gas in their process: MIG and TIG welding both use a shielding gas.
Gas Metal Arc Welding (also known as GMAW, and most commonly referred to as MIG welding) uses a wire electrode on a spool. This welding electrode is fed automatically onto the 2 ends of the weld piece that need to be joined together, and the electrical current creates an arc between the metal and wire. This is shielded by gases for MIG welding so that the arc will heat the wire to the melting point without contamination.
Gas Tungsten Arc Welding (also known as GTAW and most commonly referred to as TIG welding) uses a tungsten electrode in combination with a gas for shielding to heat the filler metal that is placed on the 2 ends of a welded piece that need to be joined together. The energy to create an arc is produced through a constant current power supply. The arc goes through a column of ionized gas and metal vapors (plasma). Again, in order to prevent welding defects due to contamination, you need a shielding gas for TIG welders.
What is the purpose of gas in MIG and TIG welding?
In MIG and TIG welding, shielding gases are necessary to protect your weld area from oxygen, nitrogen and water vapors. These atmospheric vapors will make your welding process difficult and deteriorate the quality of your weld.
Gases for shielding are gases that have more density than air. This allows them to wrap around your weld. They also don’t require flow rates of more than 15 to 20 liters per minute. These are always going to be inert or semi-inert gases.
Helium and argon are the only noble gases used in welding. TIG welding occasionally uses 100% argon in its pure form, but oftentimes these gases are blended with other semi-inter gases like carbon dioxide, nitrogen, and hydrogen to improve the characteristics of your weld in certain materials. This is especially true of helium, which lowers the weld temperature when used by itself.
There are several advantages to using gases for shielding in your welding process. These gases protect your welding arc and offer stability, allow you to use higher temperatures when welding without worrying that your material will oxidize, reduce negative effects like spatter and burn through of base material, ensure that none of the alloying elements are lost when your metal transfers across your arc, and allow you to adjust the gases to the material you are welding.
Why Gas Blending is Important in Welding
Shielding gases protect your molten weld pool from contaminants found in the atmosphere during your welding process. They remove reactive gases like oxygen and nitrogen and ensure that no water vapor contaminates your weld. They will also stabilize your arc and make sure your metal transfer is enhanced.
These can also change the basic properties of your base metal during your weld. They do this by interacting with the base and filler metals. This will change the strength, corrosion resistance, and hardness of your metals. Different gases have different properties and functions, which is why blending is important.
Hydrogen is a very cheap gas for shielding. It allows for a stable and concentrated arc. It also produces a higher arc temperature, better ignition, allows for faster welding speed, and offers a better bead surface while welding.
Argon is an affordable gas. This inert noble gas produces a stable arc. It also improves your control over your weld pool, offers better and more confined penetration, and improves the oxide breakdown, allowing you to clean your metal as you weld.
Helium is much more expensive gas. It can often produce an unstable and wandering arc but has some great benefits when mixed. The inert noble gas supplies extra heat input and improves the fluidity and penetration of your weld pool.
MIG Welding Gases
A lot of different gases and blends can be used in MIG welding, which is a pretty common and versatile technique that is forgiving of beginners’ mistakes in technique. The material you are welding will dictate what type of gas you choose.
A lot of different applications in MIG welding can use different shielding gas options. You need to determine your welding goals before choosing the right gas for your specific task. Consider the cost of the gas, the desired properties of the finished weld, the penetration and clean up, your base material, the process you’re using, and how quickly you want to move before selecting your gas.
Carbon and Low Alloy Steels
For this base material, use a blend of argon and carbon dioxide. Usually, you will want 75% argon to 25% carbon dioxide. This will increase the penetration of your weld and improve the wetting characteristics of your bead. These can also be used to join carbon steel to low alloy steels.
Nitrogen is also cheap. If you’re not careful, it will cause your arc to wander, but it can also build up nitrides in higher temperatures. Nitrogen is used as a purging gas also.
Carbon dioxide is the most common mixer gas. It’s very cheap but also produces an unstable arc. In a small ratio, it will stabilize and oxidize your arc and improve the weld bead’s wettability and offer deeper penetration.
This is the only reactive gas that can be used in its pure form without adding an inert gas for MIG shielding. It's the least expensive of all the common gases for shielding, so a lot of people like to use it. You are essentially trading a less stable arc and some extra spatter for the extremely deep weld penetration.
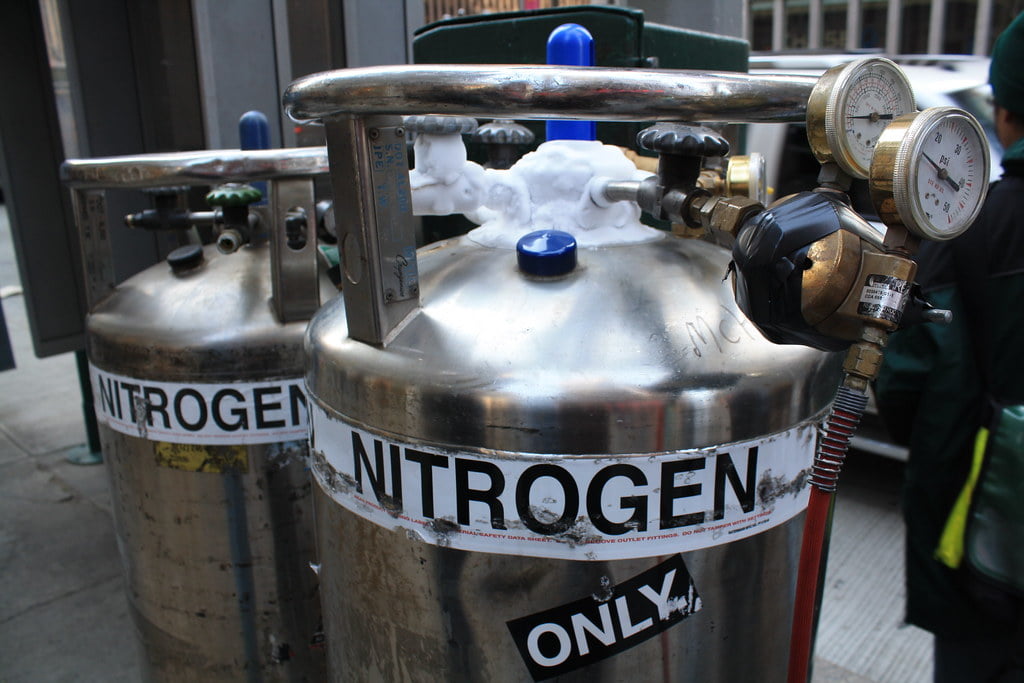
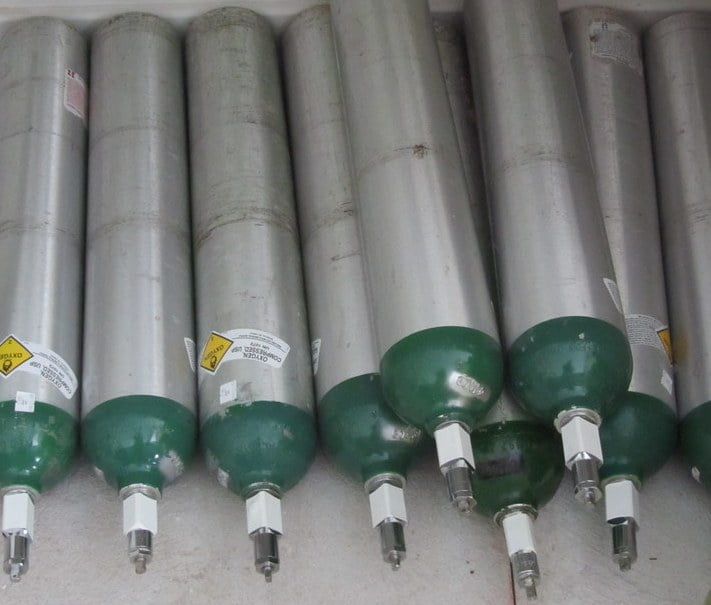
Oxygen is also cheap, but never use it by itself. In a small ratio, it can stabilize and oxidize your arc and improve penetration and weld pool fluidity.
Blends of 2 or 3 different gases for shielding are frequently used to improve the quality and efficiency of welds. These blends are tailored to specific base and filler metals for maximum impact.
Adjusting the shielding gas's composition will allow you to influence how your heat is distributed to your weld.
Adjusting the shielding gas's composition will allow you to influence how your heat is distributed to your weld. This will help to shape the weld metal cross-section and affect the speed of your weld. Increasing the welding speed can often be substantial and save a lot of labor overall.
Stainless Steel Welding Gas Mixture
For stainless steel, you may want to go with a mixture of 3 shielding gases. Argon, helium, and carbon dioxide are ideal for this welding in a 90% argon to 7.5% helium to 2.5% carbon dioxide ratio. This will allow for a stable arc and deeper fusion.
Galvanized Steel MIG Welding Gas Mixture
To MIG weld galvanized steel, use 100% CO2 in short-circuit mode because 100% CO2 creates a hotter arc to burn the zinc much faster.
If you are MIG welding thin galvanized steel up to 1/8″ (3.2 mm), use the C25 (75% argon and 25% CO2) because it creates a cooler arc.
Welding Gas for Aluminum
MIG welding aluminum can be tricky. It requires the base metal to be thoroughly cleaned, and the moment that the aluminum hits the air it begins oxidizing again immediately. For this reason, most aluminum welding requires 100% argon gas. If you’re using aluminum that is thicker than ½ an inch, you may be able to add a little Helium to increase the penetration of the heat.
Nickel Alloys Welding Gas Options
For nickel, you can use either 100% pure argon or a mixture of 60% argon to 40% helium. This will allow your weld pool to flow and improve your penetration.
Copper Alloys - Which Welding Gas Should I use?
For copper, you can either use 100% pure argon or a blend of 75% argon to 25% helium. This will allow for deeper penetration and an improved weld flow.
TIG Welding Gases
TIG welding is less forgiving of beginners. It requires a lot of experience and a very precise technique. This advanced technique is a lot more versatile, but it also takes fewer types of gas than MIG welding.
The most popular type of gas for shielding in TIG welding is 100% pure argon. This is because argon in its pure form can be used on every type of base metal, including for the notoriously finicky TIG welding aluminum.
Argon offers good stability in your arc and doesn't require as much clean up afterward because the arc is narrow and concentrated. TIG welding is all about precision, and argon produces a completed weld with a shinier surface aesthetic without bead rollover.
If you want hotter welds while you work, which allows a wider heat profile and better heat conduction, you can mix 50% argon with 50% helium.
Helium is the second most common type of shielding gas for TIG welding and frequently used in specialized projects. The extra heat also requires extra control, and you will have to use perfect technique if you want to avoid burning through your base metal.
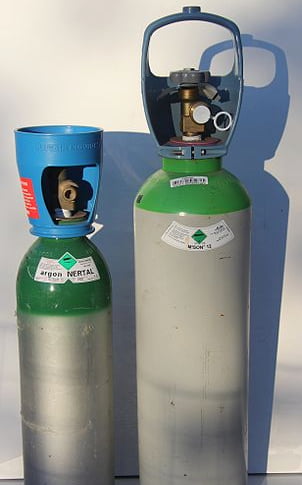
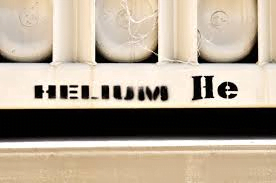
Pure helium (or a high helium mix of 90% helium to 10% argon) is another gas for shielding used in TIG welding. This mixture is usually chosen for welding with direct current electrode negative energy. (DC EN).
This combination is frequently seen in seam welding because the high input of heat from the gas provides fast welding speed and excellent penetration.
Pure hydrogen can also be used because it increases the heat output when welding, but use this with caution. It creates a hit and wide weld bead that offers deep penetration into the metal, which is great for stainless steel but requires very precise control to avoid burning through your base.
Welding Gas Use Safety Tips
These gases are difficult to identify because they are invisible. That being said, they can be toxic and harmful. These gases can burn or asphyxiate you if you're not careful. Make sure to observe safety tips when using gas.
Inspect all of your equipment for leads at every possible connection. Inspect your hoses for worn places and leaks and replace any bad hoses. Protect your hoses and gas cylinders from sparks, flames, or hot metal during welding. Use a flint to ignite the flame.
Stand away from regulators (ff to the side) when you open your gas cylinder valves.
When you do, open them very slowly so you avoid exploding regulators under high pressure. Only open acetylene cylinder valves ¼ to ¾ turn and leave your wrench in place so it can be closed again quickly.
Open and light your acetylene before you open and adjust the oxygen to a neutral flame. Close your acetylene torch valve first when you shut it off.
This might result in a pop noise as the oxygen blows out the flame, but it will remove any chance of that flame burning the acetylene line.
When you are finished, close all your gas cylinder valves, bleed the lines to remove pressure on the regulators, and coil your hoses neatly.
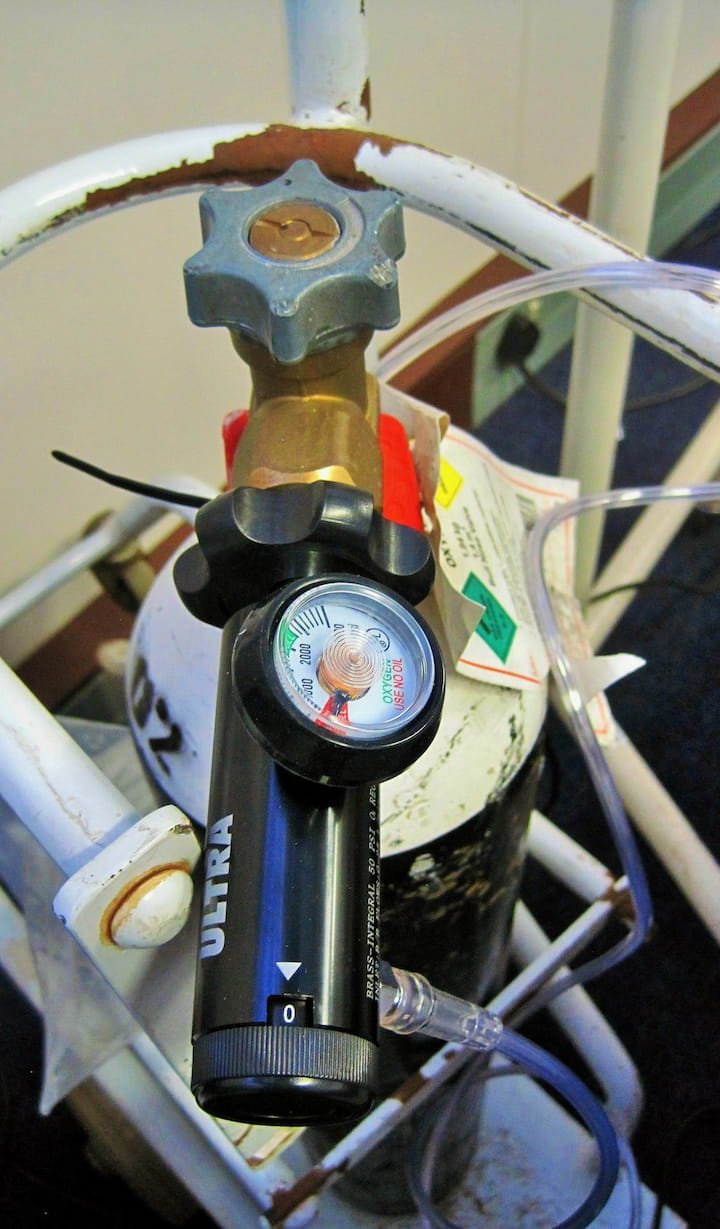
FAQs
What gas is used to shield welding?
Argon, Helium, Carbon Dioxide, and Oxygen are the four shielding gasses most frequently employed in MIG welding.
What is the best shielding gas for MIG welding?
The most popular gas for shielding at home and hobby MIG welders is 25% carbon dioxide with 75% argon gas. Although this mixture isn't inexpensive, welders prefer it because it strikes a good balance between price and completed weld quality. This gas for shielding mixture is readily offered at nearby welder supply shops.
What is C25 welding gas?
For residential and recreational MIG welding, C25 (75% argon gas and 25% carbon dioxide) is the most popular gas for shielding. It's not the most affordable gas mixture, but many enjoy it because it strikes a good compromise between price and the caliber of the end weld when someone MIG welds at home.
Why do welders use helium and argon?
Helium and argon are both quite inert (unreactive), and they both create a protective atmosphere surrounding the welding site. This is why scientists use them to safeguard reaction mixtures.
Can you use 100% argon with MIG?
Yes, you can MIG weld steel if all you have is pure Argon. This is a question that every welder will encounter at some point.