Understanding MIG vs TIG welding is a must because not all welding jobs require one and the same process. The more types of welding you master, the more materials you'll be able to work with. This also means that there will be more work coming your way that you can take and successfully complete to your employer's satisfaction or for your own pleasure if you're not a pro welder.
Table of Contents
Key Takeaways
- MIG is a lot quicker and easier to learn and the actual welding procedure is a lot quicker
- TIG welder ( tungsten inert gas ) enables you much more versatility than a MIG welder
- MIG welders ( metal inert gas ) have spool-fed wire running through the machine while TIG welders use interchangeable filler rods
- When comparing MIG and TIG welder speed, TIG welding is not nearly as fast as you have to change filler rods
- Both MIG and TIG welding requires a shielding gas during the welding process
You will especially appreciate the effort we put into writing this article if you’re a beginner. This is because we will hopefully provide you with better understanding of different welding techniques. We'll also mention the best MIG welder features as well as TIG units available and how they perform. If you don't have the desire to learn and practice, even the best TIG welder won't be of much use.
In addition, in our guide, we'll consider the importance of welding skills needed to operate different types of welders. Finally, we will outline specific applications which are best suited to different ways of welding .
Getting to know the advantages and applications of MIG Welding / Gas Metal Arc Welding (GMAW) and TIG Welding / Gas Tungsten Arc Welding (GTAW) will also determine what type of welder and consumables you need to have so when a job comes up, you just grab your gear and do your best to make the most of it. Do have welding safety in mind at all times!
Why is MIG Welding Used More Often Than TIG?
You will often hear that the MIG welding process is a lot more common than TIG welding. Why is this? Well, first off, when you consider MIG v TIG welding, MIG is a lot quicker and easier to learn and the actual welding procedure (including whether to push or pull when MIG welding) is a lot quicker. However, it's not as versatile as TIG welding.
Using a TIG welder enables you much more versatility than a MIG welder. When you are using a TIG welder, you can change the filler material in a jiff by just grabbing another rod. This means you can TIG weld different metals at high speed and complete the job without making any filler adjustments to your welder and still get great TIG welds.
MIG welders use a wire which is fed through the actual machine, so to change the welding materials you need to change the wire you're using, which is not as fast as we're talking a MIG weld pool of wire compared to TIG filler rod.
Both MIG and TIG welding are used to superheat the metals into a liquid state. Then in order to fuse them, you use a filler material. Apart from MIG and TIG welding processes, we'll also mention Flux Core (Flux-cored) and Stick welding for which you can get a combo welder to be able to weld using several methods.
We explained how to use a spot welder in a separate guide as the process differs greatly from MIG and TIG welding.
MIG vs TIG Welders- What is the Difference Between MIG and TIG Welding?
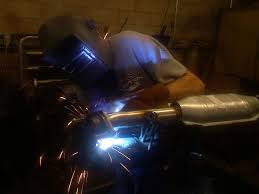
MIG Welding / GMAW uses a wire welding electrode on a spool that is fed automatically at a constant pre-selected speed.
The main difference between the MIG and TIG welding methods is that MIG welders run the filler welding material from a wire coil which is fed through the MIG torch. This wire carries the electrical current, and does the actual welding. Again, it's fed in a spool of wire right through your welder.
TIG welding involves and uses a Tungsten electrode to heat metal you're working with. A rod TIG filler is used to TIG weld two pieces together while the TIG electrode is not consumable. Why is a TIG electrode so powerful? Few people actually know that TIG electrode name originates from Swedish language where "tung", means "heavy," and "sten", meaning "stone."
In chemistry, tungsten (the T in TIG) is actually Wolfram which has the highest melting point of all the elements, melting at 6192 °F (3422 °C, 3695 K). It also has the highest boiling point, at 10706 °F (5930 °C, 6203 K). Its density is greater than that of lead and no wonder why a tungsten electrode lasts for a good while if you're operating your TIG welder skillfully. If you are new to TIG, we recommend reading our TIG Welding For Beginners post.
Another difference between the MIG and TIG welding procedures is how long you can weld in continuity. As we mentioned in MIG welding basics, MIG weld work can go on until the wire reel runs out (most quality MIG welders will run 22 pounds wire spools while smaller wire reels are available for less powerful (hobby) welders. So when comparing the speed of MIG and TIG processes, TIG welding is not nearly as fast.
Both MIG and TIG welding need a shielding gas during the welding process. This is to protect the weld from the contaminants in the environment, mainly Oxygen and Nytrogen.
Conversely, Stick welding (also known as Shielded Metal Arc Welding), does not require a shielding gas. This is why Stick welders are often used when welding outside in less than favorable weather conditions (think of welding a car exhaust pipe, a property fence or outdoor stairs.
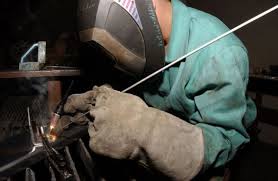
To sum up this part of our article, matching your needs and having suitable welding skills and knowledge (including what reverse polarity is, direction, angles etc) for the task at hand is super-important before moving on to specific jobs as well as various welders available for different types of welding jobs.
Overview of MIG vsTIG vs Stick Welding
The most common methods that experienced welders use are MIG welding , TIG welding and stick welding. All three have their own benefits and limitations when it comes to suitability for specific applications. If you learn, improve and master all three means you will be ready no matter what the job is. Is stick welding stronger than MIG? Yes, on thicker metals. However, MIG is a huge time saver.
All three methods require the use of an efficient, top-rated welding helmet for maximum weld quality and eyes protection.
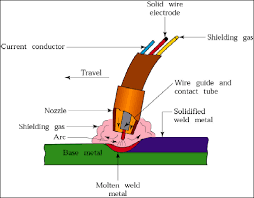
How Does MIG Welding Compare With Flux Core?
MIG Welding / GMAW process uses a wire welding electrode on a spool which is automatically fed through the MIG gun at a constant speed that you select based on the task you're about to do.
The electric arc is created by the electrical current between the metal you are welding and the wire. The current melts the wire and joins it with the base when your MIG gun welding torch is on.
This results in a high-strength weld which looks really good and needs little cleaning.
Flux-cored Arc Welding (FCAW) is similar to a MIG process in that it's also a wire-feeding process. Where it differs in that self-shielded flux-cored welding does not require a shielding gas. What is used instead is the flux-cored wire which shields the electric arc from contaminates. This makes Flux Cored welding a simple but highly efficient welding procedure, especially when you are welding outdoors and in windy conditions. This is why FCAW is most commonly used in construction due to its great welding speed and also portability.
Both MIG and flux-cored welding process are easy to learn for novice welders. From the very start, you can make extremely clean and quality MIG welds on different metals such as aluminum, mild steel, and stainless steel. Both MIG welds and Flux Cored welding will let you weld materials as thin as 26-gauge.
TIG Welding vs Stick Welding
TIG welding ( tungsten inert gas ) is also an arc welding technique. It utilizes a non-consumable Wolfram electrode which produces precise and quality TIG welds.
The weld area is protected from atmospheric contaminants by a shielding gas (25/75% argon and CO2 mixture and pure Argon also works) and a filler metal. Autogenous welds, do not require it.
The energy that is conducted across the electric arc through a column of highly ionized gas is produced by the constant-current welding power supply.
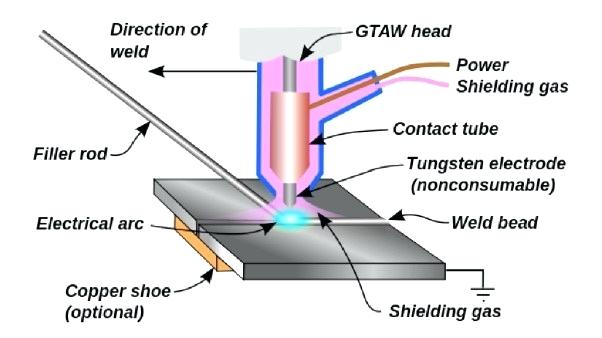
TIG welding is successfully and commonly used to weld stainless steel, thin sections of alloy steel, and non-ferrous metals such as TIG welding aluminum, magnesium and also copper alloys. TIG process gives the experienced welders a much better control over the weld than any other welding type. This allows for strong, high-quality and very precise TIG welds, but not at as high speed as MIG ( metal inert gas ).
In addition, the TIG welding process is much more complex and difficult to master than other welding techniques. It's also quite slower so when a greater production rate is needed, MIG is by far the best option.
Stick Welding — If you started welding a long time ago, you're probably familiar with an arc welding technique. Stick welding uses an electric current which flows from a gap between the metal you're working on and the welding stick, also known as the arc-welding electrode.
Although quite old, Stick welding is a really effective method for welding most alloys or joints. In addition, it can be used indoors and outdoors or in drafty areas. Stick welding is also the most economical welding method which provides the ability to create an effective weld even on rusty or in any way dirty metal plates or parts.
As for the downsides, Stick welding is limited to metals which are no thinner than 18-gauge. It also requires frequent rod changing and it emits quite a spatter. This means you'll have to clean your welds well after finishing work.
Stick welding is more difficult to both learn and use. A notable problem is how to strike and maintain an electric arc while working. Stick welders are available in AC, DC or AC/DC. Of the two, AC is more economical. Since Stick welders enable you to work on metals of 1/16 inch or thicker, Stick welders are a great options for hobbyists, maintenance workers and farmers, for example.
Here’s a great video summarizing Stick vs MIG vs TIG welding methods:
MIG vs TIG vs STICK & Flux Core Advantages
Welding Process | Advantages |
---|---|
MIG Welding |
|
TIG Welding |
|
Flux Core Welding |
|
Stick Welding |
|
What Types of Welding Best Fits Your Needs?
The best start before buying welders is to identify the types of welding projects and materials you will work with the most. Are you fixing your vintage car your dad bought? Maybe you're restoring industrial style furniture or making metal sculptures? Whatever the welding job awaits, it's wise to know which welding method is best for specific metal thickness. So, do consider MIG or TIG welding compared with other methods.
Possible Projects | Material Thickness |
---|---|
Auto body welding | 3/16-inch or less |
Around the farm/ranch/yard | 5/16-inch to 3/8-inch |
Thick structural components | 3/8-inch or more |
Bicycles or any tubes/pipes | 1/16-inch |
Boats, cars and motorcycles | 1/16-inch to 1/8-inch |
Hunting stands and utility trailers | 1/16-inch to 1/8-inch |
General to heavy repairs | 3/16-inch to 1/4-inch |
How To Determine the Budget for Buying MIG vs TIG, Stick and Flux Core Welding Gear and Accessories?
Do not waste your money: think about MIG vs TIG welding gear when deciding on your purchase so that the unit suits your specific needs in terms of functions and features for the projects you will work on the most.
Think about your end goal and consider which type of welder will be the most useful so that you can do as many welding jobs as possible.
You also need to consider the various amperage and power requirements as well as the welder duty cycle which is needed to achieve the most effective but also most economical results for the projects you’re planning to complete as a pro or hobby welder.
Apart from the cost of the MIG welders, TIG welders, Flux Core or Stick welders, you should consider the costs for all accessories and supplies you’ll need to operate your new welder efficiently and safely.
Include welding protection accessories such as the auto darkening welding helmet, gloves, apron, jacket and spare parts for your welder and welding torch. Do not forget electrodes and gas which are consumables that need to be bought over and over again.
If you plan your budget according to your needs and the welding jobs you are aiming for, you will pay off your MIG and TIG welder and other gear soon, either as a professional welder or as a hobbyist.
One thing is sure, there is no shortage of great quality TIG welder models and MIG welding equipment for every skill level and every type of welding work, so choose wisely, follow the safety procedures and start welding!
FAQs
1. Is TIG better than MIG?
TIG welds ( tungsten inert gas ) are preferable for smaller projects and thinner metals because they result in accurate and clean welds. Larger projects requiring longer, continuous runs and thick metals respond well to MIG welds ( metal inert gas ). TIG welders need to be able to balance materials in both hands and work with timing.
2. Is MIG or TIG welding harder?
TIG welding is harder than MIG welding. It is generally acknowledged that MIG welding is less complicated and more straightforward to learn than TIG welding. The MIG process is faster than TIG due to its continuous feed.
3. What is better for welding aluminum TIG or MIG?
For aluminum welding, GTAW (TIG) and GMAW are typically employed (MIG). Because TIG provides for better outcomes on lighter gauge materials, the majority of experienced welders in the industry agree that it is the preferable option for welding aluminum. TIG welding aluminum can result in high-quality welds when done properly.
4. Which is cheaper, TIG or MIG?
The MIG welding technique is more economical than TIG, because it is so much faster. MIG parts are also easier to get and far less expensive than TIG ones. TIG welding costs more per foot of bead because the deposition rate is lower.
5. What type of welder is best for a beginner?
The best sort of MIG welders for beginners are those that have a wire welding electrode on a spool that is fed through a welding gun at a predetermined speed. GMAW or MIG, which is an automatic or semi-automatic procedure, is the simplest to learn.