Are you looking for an efficient, cost-effective way to weld stainless steel? You may be wondering if flux core welding is the answer, but can you weld stainless steel with flux core?
Depending on the specific type of project you’re working on, using flux core to weld stainless steel can be a highly effective solution – and it comes with a range of benefits that make it worth exploring. In this blog post, we’ll look at the ins and outs of welding stainless steel with a flux core welder so you have all the information you need to decide if it’s right for your next project.
Table of Contents
Key Takeaways
- Although you can weld stainless steel with flux core, it is not commonly used in the field, and no experienced welder would recommend this.
- Using flux core to weld does not require shielding gas, so it can be a go-to for a quick weld
- Used for making welding a faster process, but only if it is for an outside project
- It can be the most efficient method out of others.
Main Categories of Stainless Steel
When welding stainless steel, it’s important to understand the different available types of stainless steel. From what I have researched, stainless steel can be divided into four main categories: austenitic, ferritic, martensitic, and duplex.
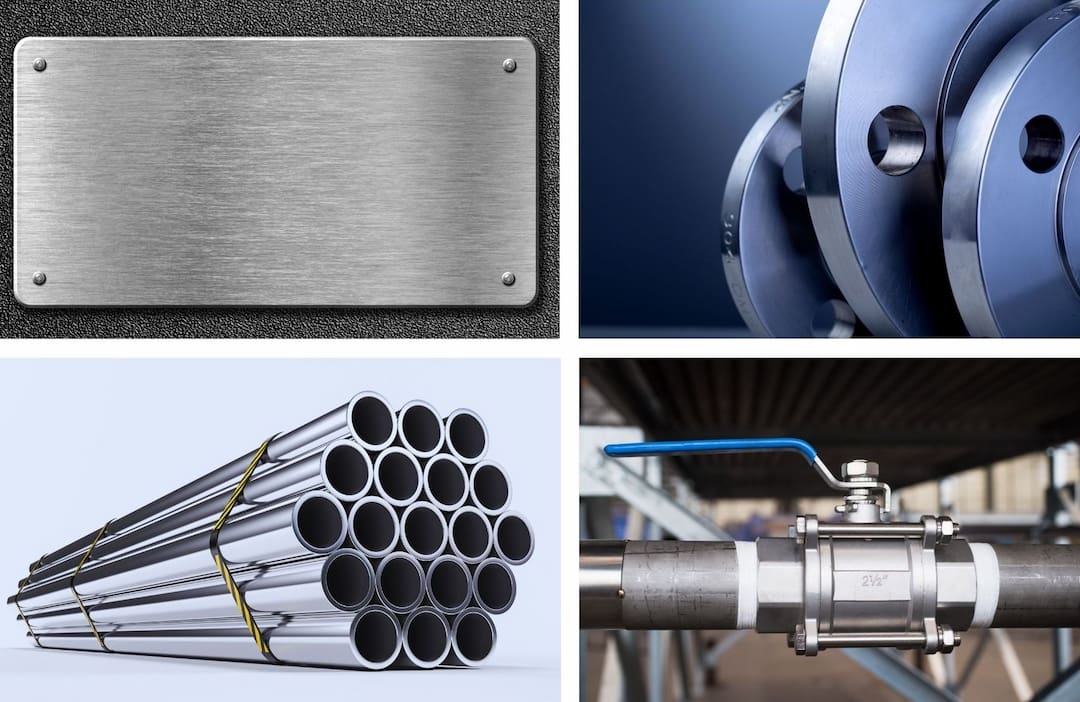
Austenitic: This type is non-magnetic and highly corrosion-resistant. The majority of stainless steel products are made from austenitic stainless steel, making it the most popular choice for welding.
Ferritic: Ferritic is magnetic and has good corrosion resistance. It’s often used in automotive applications and appliances such as stoves or refrigerators.
Martensitic: This type is also magnetic and has good corrosion resistance. It’s typically used in cutlery, knives, and other tools.
Duplex: It is both magnetic and highly corrosion-resistant. It’s often used in chemical processing facilities and offshore oil rigs.
Welding Stainless Steel with Flux Core
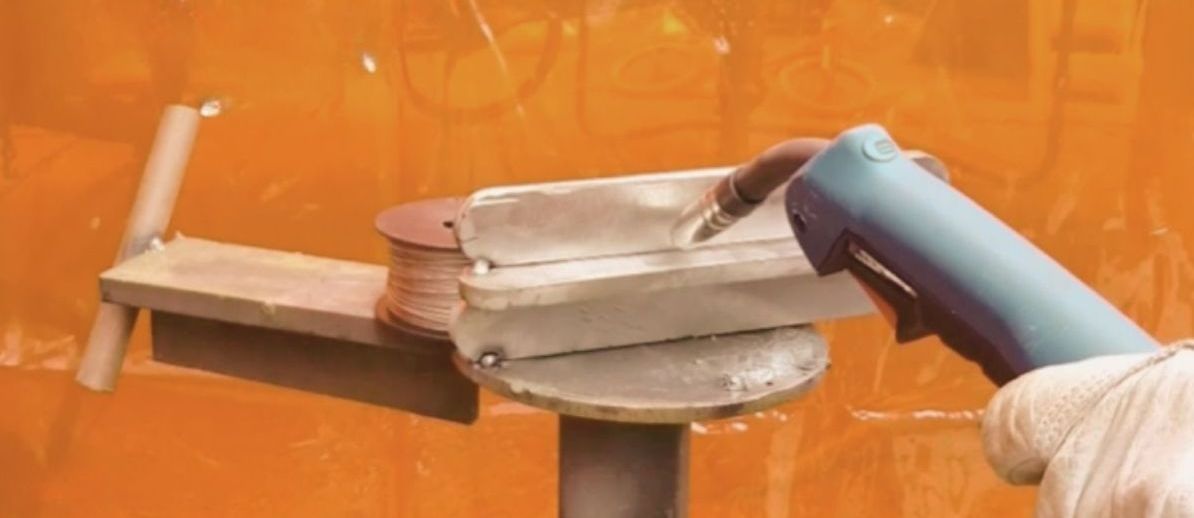
Welding stainless steel with flux core can be extremely beneficial for certain projects. Flux core welding is a semi-automatic process using self-shielded wire and an external shielding gas to create strong and reliable welds. It’s also faster and more efficient than other welding methods, making it ideal for high volume, so I highly recommend it. It’s a great solution for outdoor welding projects since the self-shielded wire doesn’t require an external shielding gas to work effectively.
When deciding whether to weld stainless steel with flux core wire, it’s important to determine the type of stainless steel you are working with and be aware of the advantages and disadvantages of the welding process that might concern you.
How Flux Core Welding Works?
This process provides a higher deposition rate than many other forms of welding, making it ideal for thicker pieces of metal and larger projects. The arc produced by flux core welding also produces less spatter, making it an ideal choice for those welding in confined spaces or tight areas.
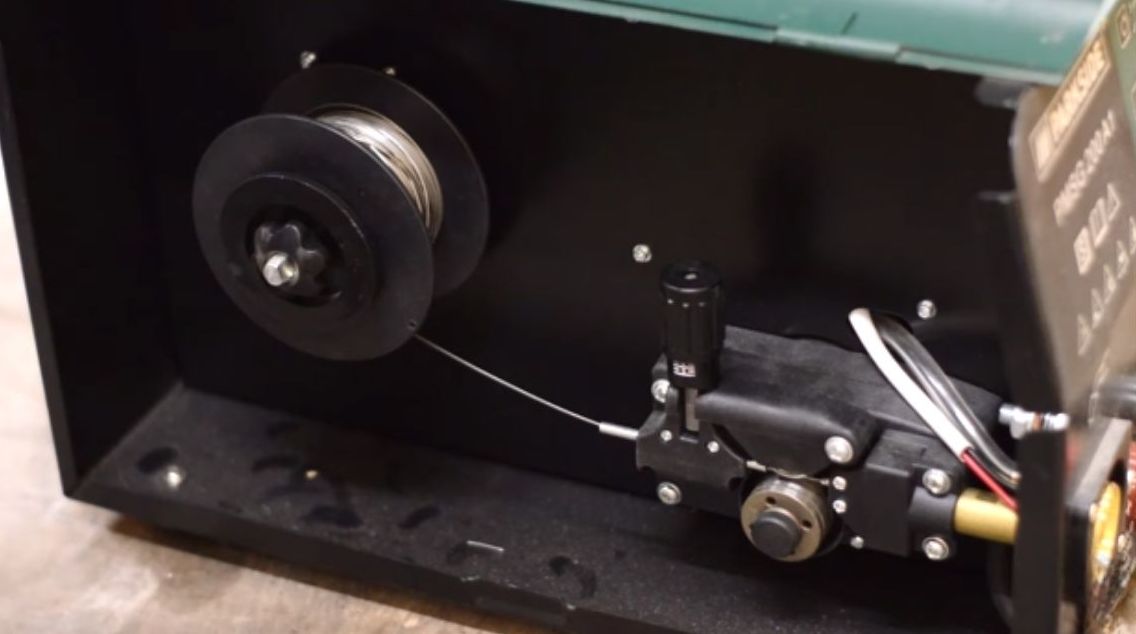
Flux core welding wire is also a self-shielded process, meaning there is no need to use a shielding gas when performing this type of welding. This makes flux core welding easier and safer because you don’t need to use shielding gas tanks and worry about the associated risks.
The flux in the wire's core serves as a shield, protecting the welders from dangerous fumes. It also helps clean any contaminants on the metal before welding begins. It contributes to better arc stability, which is essential for producing quality results.
To perform flux core welding, the welder must ensure the metal is properly prepared by cleaning it and removing rust or dirt. Once the area has been cleaned, a flux-core wire is inserted into the electrode holder and connected to the power supply.
Once everything is ready, you can adjust the settings on your welder to the correct amperage for your project and then begin welding. You can keep a steady speed and the arc length consistent as you weld.
Advantages Of Welding a Stainless Steel With Flux Core
- Flux core welding is ideal for large projects and thicker stainless steel rods. It’s a fast, efficient process that produces fewer fumes than other methods, making it safer. The self-shielded wire also means there is no need for an external shielding gas, saving you time and money.
- Flux core welding with stainless steel is easier to use and poses fewer operational risks than other welding processes. This makes it ideal for welders of all levels, from beginner to advanced.
- Flux core welder also produces a smooth, consistent weld bead which can be aesthetically pleasing for certain projects. The process allows you to make deep penetration welds with minimal heat input, reducing the risk of warping and distortion.
- With flux core welding, you can also produce stronger welds in less time than other methods, saving time and effort. The process is relatively low maintenance compared to other welding processes, as no shielding gas needs to be changed or replaced.
Disadvantages of Welding a Stainless Steel With Flux Core
- Flux core welding is a more specialized process than other forms of stainless steel or filler metal, requiring more experience to be done correctly. Incorrect use of flux cores can lead to poor welds that can cause leaks or structural failure over time.
- The flux core wire itself adds additional costs to the welding process. Not only is there the price of the flux core itself, but also the cost associated with disposing of it afterward.
- Flux core wire welding can produce a lot of smoke and spatter, which can be a nuisance and lead to an unpleasant working environment for welders. This can be especially problematic in enclosed spaces requiring more than ventilation and air filtration.
- Flux core welding can also decrease the stainless steel's overall strength, flexibility, and corrosion resistance due to contamination from the flux core wire. Depending on the grade of stainless steel you are working with, this can be a major concern.
- For welding stainless steel to mild steel, we recommend TIG welding for best results.
What To Consider While Welding Stainless Steel With Flux Core?
Before attempting to weld with a flux core wire, several things must be considered for a safe and successful welding operation.
Joint Preparation: It is essential to properly prepare joint surfaces before welding stainless steel with a flux core wire. This includes cleaning the surface and removing any oxidation or contaminants. Proper joint preparation will help ensure a more even weld bead and create better material penetration.
Amperage Settings: Stainless steel requires higher amperages than other materials, so it is important to ensure that your welder is set correctly for welding stainless steel with a flux core wire. It is also important to note that the amperage settings should be manageable as this can cause burn-through and other damage.
Shielding Gas: When welding stainless steel with a flux core wire, it is important to use a shielding gas. This will help protect the weld area and provide better arc stability when striking an arc.
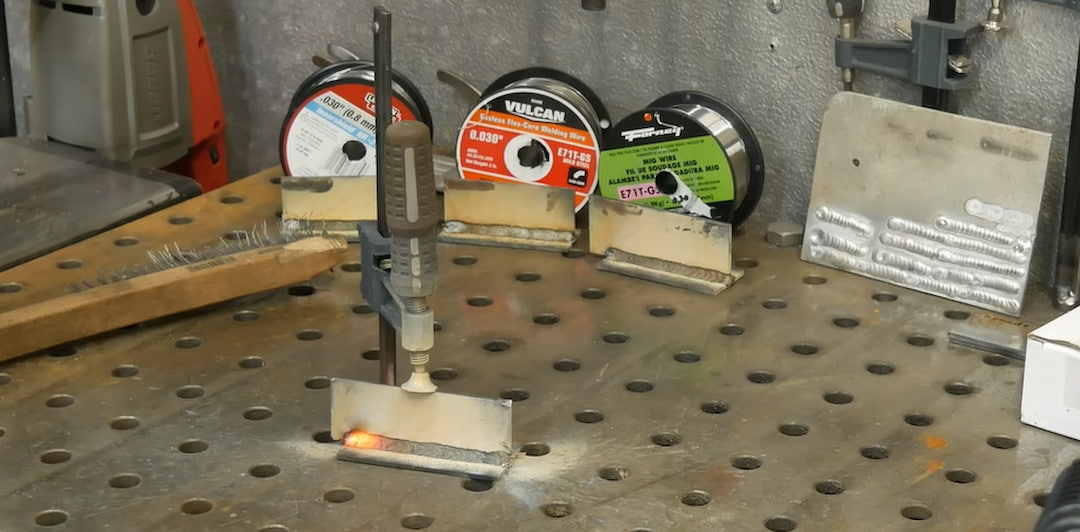
FAQs
What flux to use for stainless steel?
Different types may be used when welding stainless steel with flux-cored wire. Generally, the type of flux-cored wire that is selected will depend on the grade and thickness of the stainless steel being welded. An all-position E309LT-1 flux-cored wire is a good choice for most grades and thicknesses. It can be used for welding stainless steel to carbon and low alloy steels and joining dissimilar metals. For thicker sections of stainless steel, an E308HT-1 or E316LT-1 flux-cored wire may be needed.
Can you weld stainless steel with a MIG welder flux core wire?
Yes, it is possible to weld stainless steel with a MIG welder flux core wire. However, special care must be taken to ensure the right welding technique is used for successful results. In most cases, pulsed MIG welding is recommended when welding stainless steel with a flux core wire, due to its increased ability to provide deeper penetration and better weld control.
What metals can you weld with flux core?
Flux core welding is most commonly used for welding mild steel and low alloy steel. It can also be used for other metals, such as stainless steel, as we have discussed in this article, remaining Chromoly, and aluminum. This type of welding is ideal for outdoor applications, as it does not require a shielding gas.