Today, we will offer an overview of welding vs brazing so that you have all the information necessary to decide which process might be best for your project. We'll discuss the key differences between welding and brazing, their advantages/disadvantages, the materials used, and other important considerations.
Table of Contents
Welding and brazing are common techniques for fitting two metal parts together. However, there is a big difference between the two processes, making it difficult to decide whether welding or brazing should be used in a given situation.
What is Welding?
Welding is a process of joining two or more pieces of metal together by heating them to their melting point and then applying pressure. During the welding process, filler metals (solid or liquid) are used to create strong weld joints between the two base metals.
Welding processes require high heat and pressure, making it one of the more difficult techniques for joining two pieces of metal. Furthermore, welding often requires specialized and more expensive tools than a brazing torch.
To start with, you will probably need a good MIG welder, a reliable stick welding machine, or a multi process welder that can handle the above two processes but can be also used as a quality flux core welder.
You will also need welding rods or wire as well as shielding gas in case of gas arc welding methods such as GMAW: MIG (Metal Inert Gas) welding, MAG (Metal Active Gas) welding, and GTAW: TIG (Tungsten Inert Gas) welding.

What is Brazing?
Brazing is a process of joining two materials together by using filler metals. It works similarly to welding but uses different materials and temperatures than welding does. During brazing, the base material is heated until the filler metal liquefies and flows into the joint between the two pieces being joined. Upon cooling, solid joints are formed.
Brazing is especially useful for joining metals, such as aluminum and steel, because the filler metal used during brazing is usually lower in melting point than the base materials being joined. This allows for a much wider variety of material combinations to be joined without fear of damaging either piece due to overheating.
Compared to welded joints, brazed joints typically feature higher flexibility and may be stronger depending on the filler metal used. However, brazed joints are not as strong as welded joints and are more susceptible to fatigue failure over time.
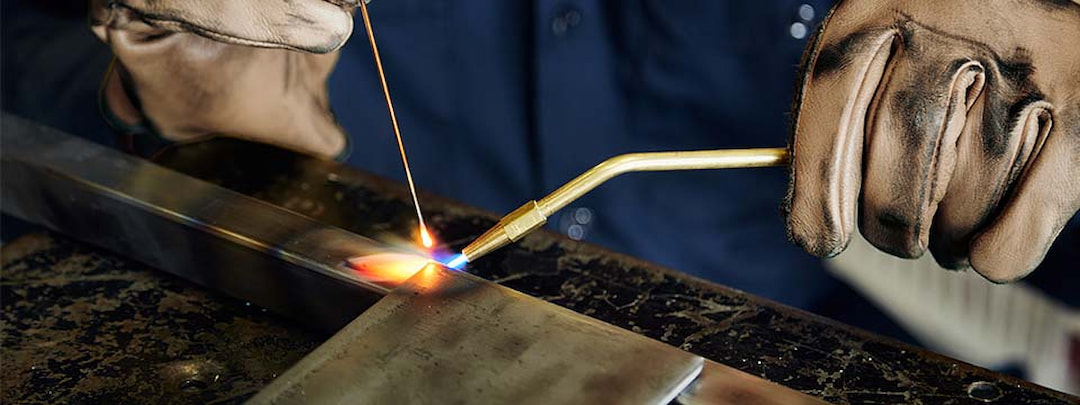
Base Metal | Brazing Filler Metal |
---|---|
Aluminum | BALSi, alluminum silicon |
Carbon steel | BCuZn, brass (copper-zinc) BCu, copper alloy BAg, silver alloy |
Alloy steel | BAg, silver alloy BNi, nickel alloy |
Stainless steel | BAg, silver alloy Bau, gold base alloy BNi, nickel alloy |
Cast iron | BCuZn, brass (copper-zinc) |
Galvanized iron | BCuZn, brass (copper-zinc) |
Nickel | Bau, gold base alloy BAg, silver alloy BNi, nickel alloy |
Nickel-copper alloy | BNi, nickel alloy BAg, silver alloy BCuZn, brass (copper-zinc) |
Copper | BCuZn, brass (copper-zinc) BAg, silver alloy BCuP, copper-phosphorus |
Silicon-bronze | BCuZn, brass (copper-zinc) BAg, silver alloy BCuP, copper-phosphorus |
Tungsten | BCuP, copper-phosphorus |
Common Features of Welding and Brazing
Both welding and brazing involve joining two metal pieces with a welded joint. To do this, localized heat is generated and applied to the base materials (the two metals that need to be connected). This heat melts the base materials, allowing a filler material (a third metal) to flow between the pieces and join them together while cooling.
The type of filler material and welding process used will determine the characteristics of the welded joint, such as strength, durability, and heat resistance. Both welding and brazing involve applying localized heat to a base material and inserting a filler material; however, they differ in terms of the type of filler materials used, the amount of heat required, and other factors.
Advantages and Disadvantages of Both Processes
Welding and brazing both have advantages and disadvantages when joining two metals together. Generally speaking, welding requires a higher melting temperature than brazing or soldering, making it more suitable for joining dissimilar metals. Additionally, welding produces a stronger joint than brazing or soldering.
On the other hand, welding requires concentrated heat to be applied, and it cannot be easy to control the results when using this technique. It is also more expensive due to the specialized equipment needed.
Brazing and soldering are cheaper and simpler than welding, making them attractive alternatives for some applications. They require less heat, making it easier to control the results. However, brazing and soldering can only join metals that are similar in composition.
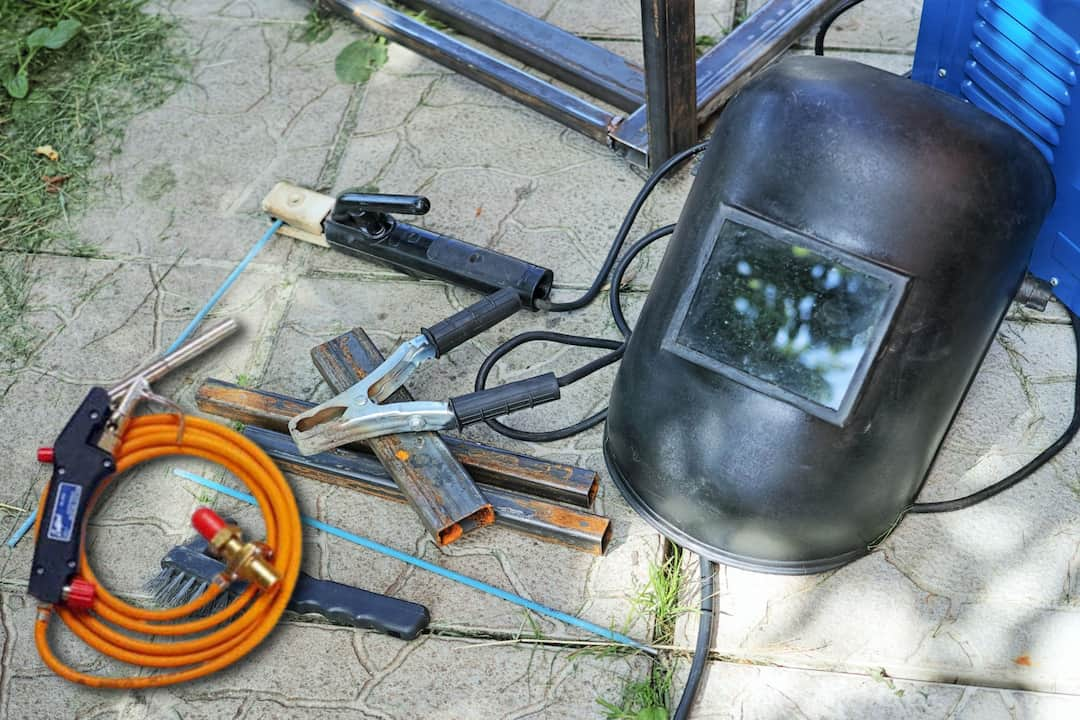
Differences Between Welding and Brazing
Welding and brazing are two different processes used to fuse metals. Each process has its unique advantages and disadvantages that can make it better suited for certain applications than others.
The major differences between welding and brazing include the temperatures used in each process, the welding methods available, and the materials used. (We covered welding vs soldering in a separate post).
When it comes to welding temperatures, welding requires much higher temperatures than brazing. This is because welding uses an electric arc or a flame to heat and melt the metals. Brazing does not involve melting the metals, so its typical temperature range is between 1,000 and 1,500 degrees Fahrenheit, lower than that of welding.
In terms of welding methods, there are a variety of different processes available. These include gas welding, arc welding, and tungsten carbide fusion. Brazing generally consists of the welding filler metal being melted by a torch or an electric current to form an alloy between two pieces of base metal.
The materials used in each process also differ significantly. Welding typically requires metals with a higher melting point, such as steel or aluminum. On the other hand, brazing can use lower melting points of metals and alloys like brass and bronze. It is also important to note that some special fluxes may be required for certain metals during brazing operations.
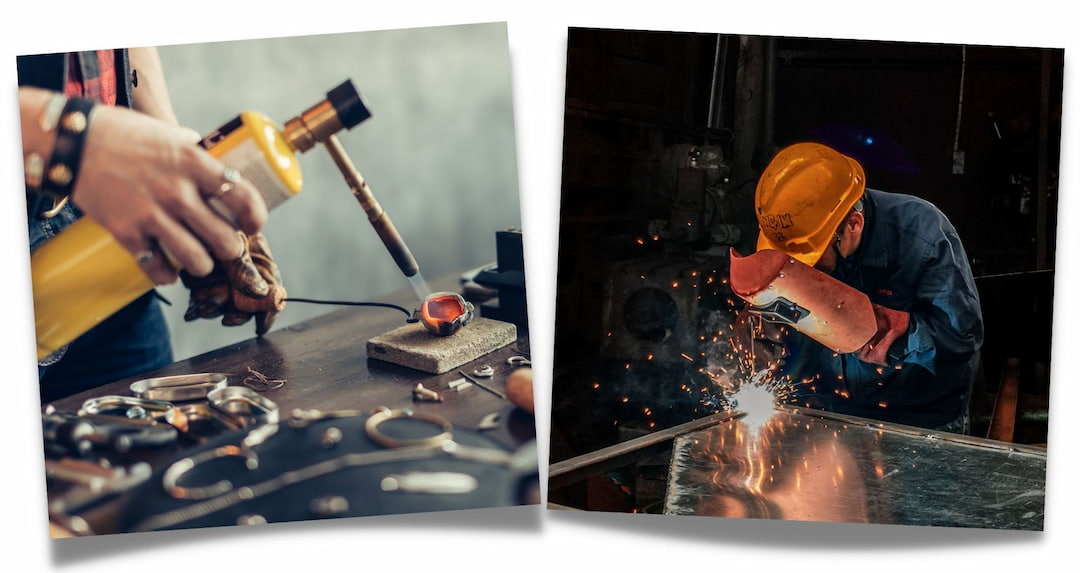
FAQs
Why choose brazing over welding?
Brazing is often preferred over welding for joining metal pieces, as it can provide a strong bond without requiring high heat or specialized equipment. When brazing, a filler metal is melted to join two metal pieces; this filler metal typically has a lower melting point than the metals being joined. This makes brazing faster and easier than welding while providing a strong bond. However, welding for joining metal pieces with high joint strength or joining metals with high-temperature requirements is more effective than brazing.
What is the difference between brazing and TIG welding?
In brazing, a filler material (usually a metal alloy) is heated to its melting point and then applied between two base metals at the joint area. The filler metal has a lower melting temperature than the base metals, so it melts and fuses them without melting the base metals. On the other hand, TIG welding is a type of arc welding that uses an electric current to create heat and melt filler metal and the base material. The filler metal for TIG welding may differ from that used in brazing and typically has a higher melting point than either of the base metals.
Is brazing better than welding?
Brazing and welding are two distinct processes that have different use cases. Brazing combines two pieces of metal using heat and filler materials at temperatures below the melting point of both base metals. Welding, on the other hand, involves melting both pieces of metal with an electric or gas flame to create a joint. Depending on the application, one may be better than the other. But generally, welding is stronger and offers more flexibility regarding design options. However, brazing has advantages as it is less expensive, can join dissimilar metals, and requires lower temperatures (brazing temperatures are typically between 800 to 1100 °F). It's best to consider both processes when deciding which one to use.