Are you in industrial manufacturing and looking for a reliable welding process? Vertical welding could be your answer. This form of welding has become increasingly popular among industrial manufacturers for many reasons, including its cost-effectiveness and ease of use.
Table of Contents
In this two pieces of blog post, we'll explain what vertical welding is, why it's important to industrial applications, and discuss the benefits they can experience by using this method.
We’ll also cover some safety tips to remember when using vertical, different welding positions, different techniques for welders, and a few potential drawbacks when utilizing this technique. So let's get started learning more about vertical welding.
What Are the Benefits of Vertical Welding?
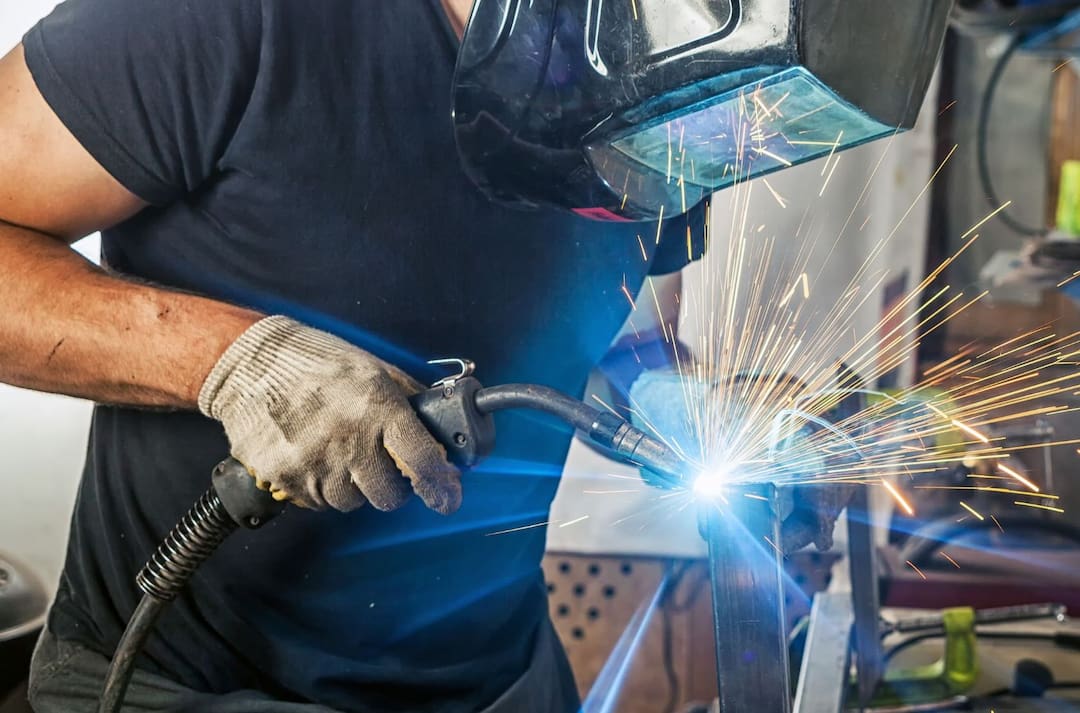
The vertical front welding technique has several important benefits, making it an ideal choice for industrial applications. Firstly, this welding type is extremely cost-effective compared to other welding processes.
This vertical up weld is typical because no additional equipment or supplies are needed to get started on welds up in vertical position, you only need the proper welder, electrodes, and welders' gloves. Secondly, vertical welding is a relatively easy process to learn and execute.
Even those with limited experience with horizontal welding position one can quickly acquire the necessary skillset for this type of two-welding position, with minimal practice and instruction. Another advantage of vertical welding position two is that it can be used in tight spaces.
This makes flat welding position ideal for applications where access to certain areas may be difficult or impossible. Additionally, flat position and the same techniques as vertical welding can be used with various metals such as stainless steel, aluminum, and copper alloys.
How Do You Weld a Vertical Joint? Do You Vertical Weld up or Down?
When welding a weld vertical joint, it is important to remember that the leading edge of the weld should move in one direction. This means that the welder needs to start at the bottom edge of the weld joint and work their way up.
This is known as “welding up” and helps ensure the weld puddle flows properly for optimal results. Additionally very good weld puddle up, it is important to keep the welding arc in a straight line to minimize any warping or distortion of base metal weld bead in the material. It is also critical to remember that vertical welds should be made with short weld beads rather than long continuous runs groove weld together, which can lead to too much heat being applied to the weld joint.
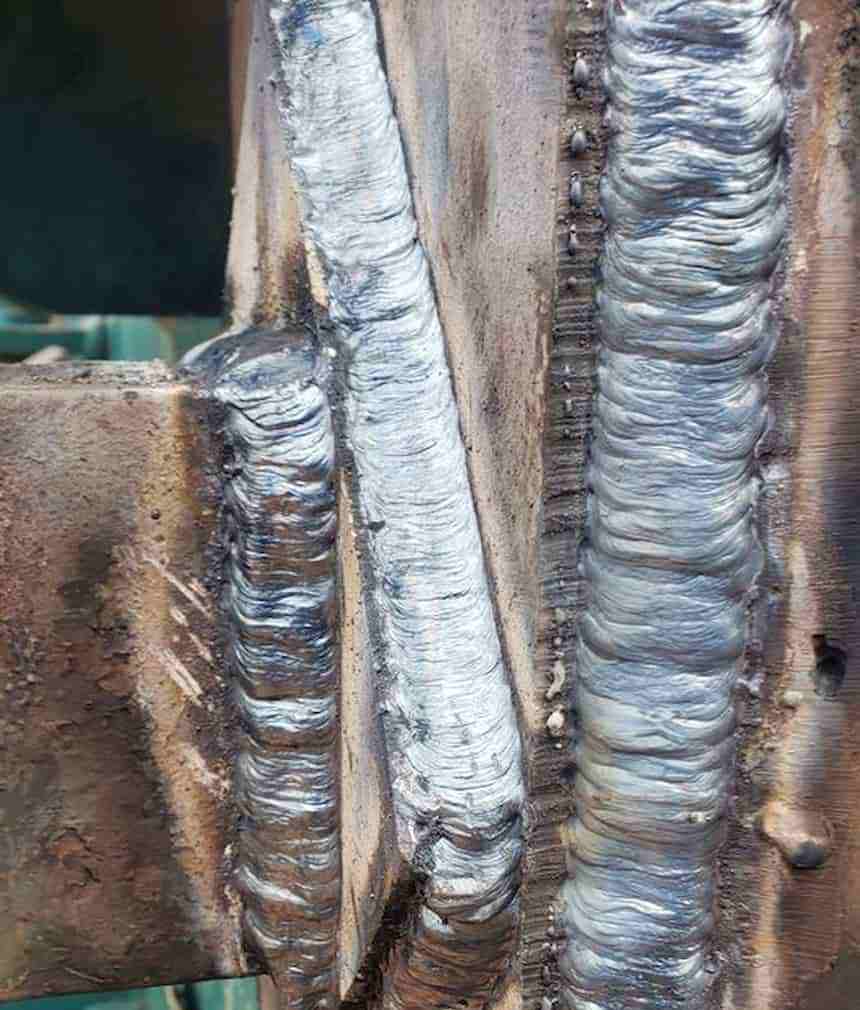
1. Vertical Up Welding:
This is the most common type of vertical up MIG welding and involves the movement of the arc in an upward direction toward the lower end of the joint. The goal is to create a flat, continuous horizontal weld line along the joint's length while ensuring no gaps, edges, or weak points are left behind.
2. Vertical Down Welding:
On the opposite side, the vertical down welding technique involves the horizontal movement of the arc in a downward direction towards the edges of the joint. This method is a technique typically used when working with thicker materials and requires greater precision to ensure an even weld line.
Welding Processes That Work for Vertical Welding
The two main welding processes used for vertical welding are Shielded Metal Arc Welding (SMAW) and Gas Tungsten Arc Welding (GTAW). SMAW is the more common of the two and involves attaching a two-stick welding electrode to the welder’s gun.
This process is highly versatile and can be used on metals of different metals in various positions. GTAW, on the other hand, utilizes metal, a tungsten electrode, and an inert gas to form the weld. This process is more precise than SMAW and normally yields cleaner results.
Equipment Needed for Vertical Welding
The minimum equipment needed for vertical welding positions includes a quality welder, safety gear such as gloves and protective eyewear, electrodes, and an appropriate welding table. It is important to ensure that the power source used in the vertical welding position is of sufficient capacity for the job at hand.
Some welders may use a jig or fixture system when welding vertically. This helps weld to ensure the joint remains in place throughout the process of stick welding and reduces any chances of warping or other issues.
When purchasing a welder for vertical side welds, overhead welding, or horizontal welding either, it is important to consider the type of material being welded and the thickness. This will help determine the kind of power source needed and any additional features necessary for the job.
Safety gear should also be a priority when selecting equipment, as it helps maintain control and protect workers from the heat and fumes generated during welding.
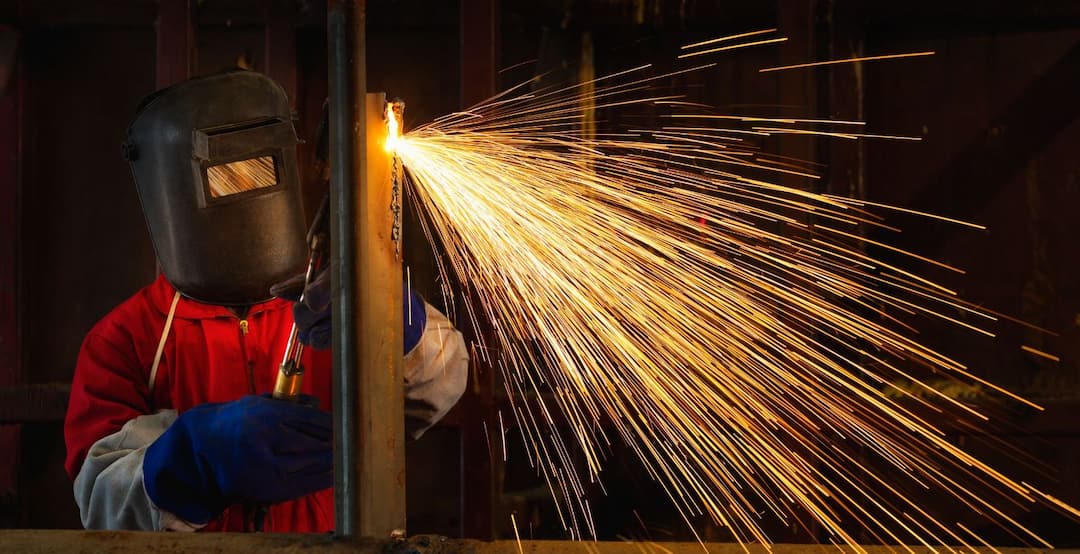
Safety Precautions & Common Mistakes to Avoid While Doing Vertical Welding
Industry professionals should follow all safety protocols and use the appropriate protective gear when performing vertical welding. This includes wearing flame-resistant clothing, a face shield or goggles, and heavy-duty gloves.
Additionally, be sure to have fire extinguishers in easy-access locations in an emergency. Furthermore, ensure that any cables and electrodes are securely connected before beginning the welding process.
One of the most common mistakes while vertical welding is not factoring in how gravity affects the flat or horizontal position of the molten filler metal and weld pool. Proper consideration allows the molten metal and weld pool to be pulled upside down and away from the joint, creating strong spots or even complete failure.
Remember that the stick electrode in the top edge of the welding arc should remain as straight, flat position, and consistent as possible during vertical up welding; any electrode deflection will cause overlapping electrode layers or insufficient penetration.
FAQs
What are the benefits of vertical welding?
The main benefits of vertical welding include cost-effectiveness, ease of use and learning, access to tight spaces, the ability to work with various metals, better penetration, and faster completion times compared to traditional flat and horizontal welding methods.
What type of welders can be used for vertical welding?
Vertical stick welding is the most common welding process used for vertical welds. This type of welding is especially useful for joining two heavy plates together or when a fillet weld must be made in a narrow space. It can also be used to create butt joints between two parts.
MIG welding is another type of welding that can also be used for making vertical welds. This type of welding is often preferred for its faster speeds and cleaner finish. However, it requires more setup time and the use of shielding gas to protect the weld from contamination. Fillet welds are most commonly used when two parts need to be joined at right angles. Since vertical stick welding does not provide good penetration for fillet welds, MIG welding is usually the preferred method. With this process, the shielding gas helps to ensure a clean and uniform weld bead by preventing oxidation along the edges of the weld.
How can vertical welding be overcome?
Vertical welding can be overcome by the welding parameters considering the effects of gravity on the flat position of the molten metal, filler metal, and weld pool. The welding arc should remain straight and consistent to prevent overlapping layers or insufficient penetration of filler metal.